Precision Injection Moulding: Revolutionizing Metal Fabrication
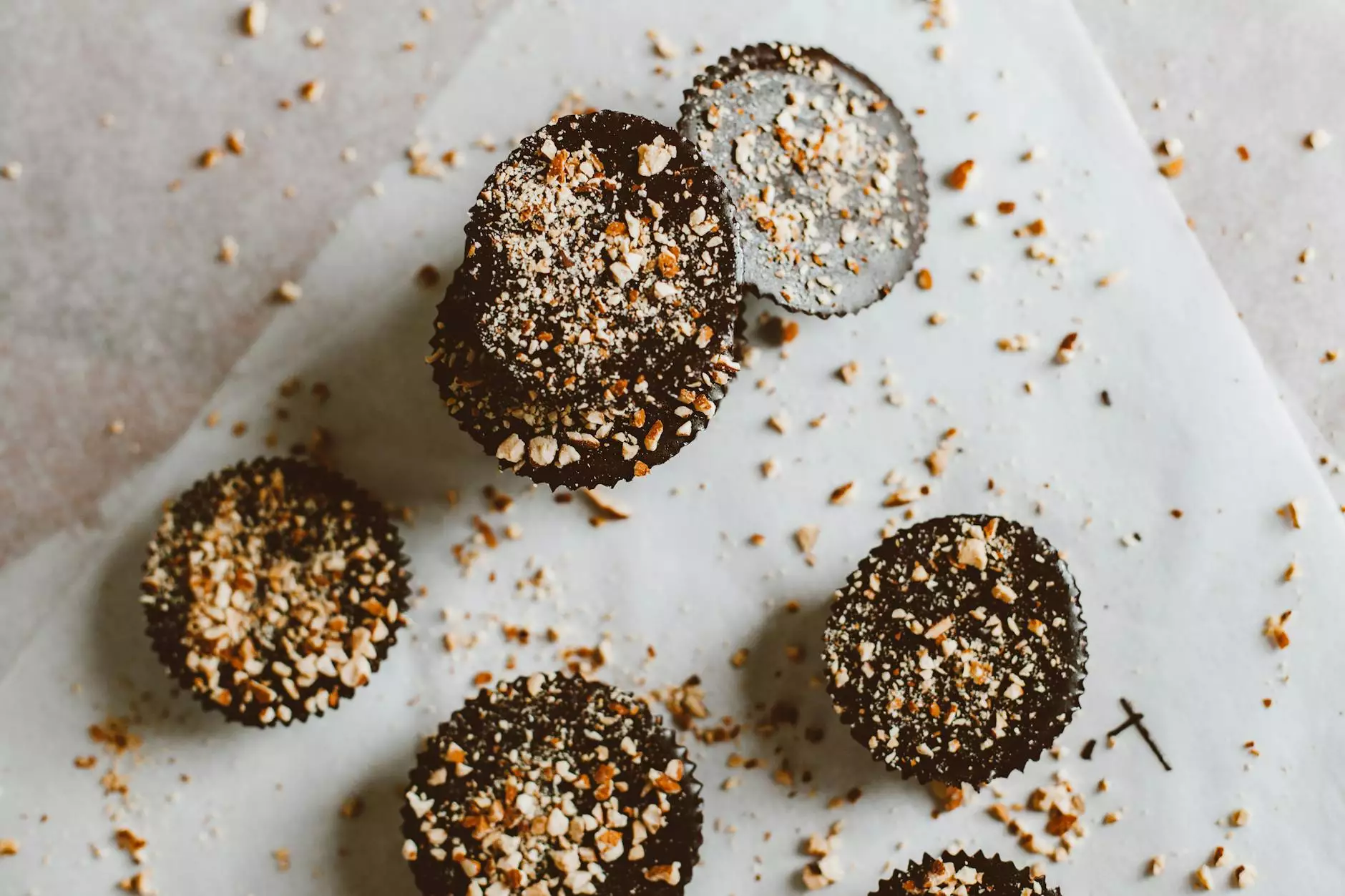
In today's fast-paced manufacturing landscape, precision injection moulding stands out as a pivotal technology that enhances efficiency, reduces waste, and optimizes production processes. As a critical component in the realm of metal fabricators, understanding the nuances of precision injection moulding can provide businesses with a significant competitive edge.
What is Precision Injection Moulding?
Precision injection moulding is a manufacturing process that involves injecting molten material into a mould to produce parts with high accuracy and consistency. This technique is primarily used for creating complex shapes and designs that are often required in modern industries such as automotive, aerospace, electronics, and consumer goods.
The Importance of Precision in Manufacturing
At the heart of successful metal fabrication lies the need for precision. The high-quality standards demanded by industries today necessitate that manufacturers adopt advanced technologies like precision injection moulding to ensure their products meet rigorous specifications. The benefits include:
- Enhanced Accuracy: Precision injection moulding allows for tight tolerances, ensuring that components fit together exactly as intended.
- Consistent Quality: Each injection cycle produces identical parts, which helps in maintaining consistent product quality.
- Reduced Waste: The efficiency of the moulding process minimizes scrap and rework, leading to cost savings.
- Complex Geometries: This method can produce intricate designs that would be challenging or impossible to achieve with traditional fabrication techniques.
Applications of Precision Injection Moulding
Precision injection moulding is utilized across various sectors. Below are some prominent applications:
1. Automotive Industry
In the automotive sector, precision injection moulding is used to manufacture components such as dashboard assemblies, gear knobs, and internal brackets. The ability to produce lightweight yet durable parts contributes to fuel efficiency and overall vehicle performance.
2. Aerospace Sector
Precision parts must adhere to stringent safety and performance standards. Injection moulding is essential for creating components like housings for electronic systems, brackets, and intricate engine parts that meet the industry’s rigorous specifications.
3. Electronics Manufacturing
The electronics industry relies heavily on precision injection moulding for producing housings for various devices, circuit board components, and connectors. The precision of moulding ensures that even the smallest parts are manufactured to exact specifications.
4. Consumer Goods
Household products ranging from kitchen appliances to toys often use precision injection moulding. The flexibility it offers in design and the variety of materials that can be used ensure that manufacturers can meet consumer demands effectively.
Materials Used in Precision Injection Moulding
Precision injection moulding can utilize a variety of materials, including:
- Thermoplastics: Commonly used for their adaptability and ease of processing.
- Thermosetting Plastics: Known for their durability and resistance to deformation.
- Metals: Certain alloys can be injection moulded, expanding the application scope significantly.
- Composites: Combining materials to leverage their unique properties, enhancing performance and stability.
Advantages of Using Precision Injection Moulding
The adoption of precision injection moulding in metal fabrication comes with multiple advantages, including:
1. Cost-Effectiveness
While the initial setup for injection moulding can be high, the long-term savings in manufacturing costs, reduced material waste, and speed of production often outweigh the initial investment.
2. Speed
Precision injection moulding is designed for high volume production. Once the moulds are created, parts can be produced in a fraction of the time it takes with traditional manufacturing methods.
3. Versatility
This process can be employed to create parts from different materials, accommodating the diverse needs of the market.
The Future of Precision Injection Moulding
The landscape of precision injection moulding is continuously evolving. Innovations in technology, such as the incorporation of 3D printing in mould design, and advancements in materials science are paving the way for enhanced capabilities.
Embracing Industry 4.0
As businesses adapt to Industry 4.0, the integration of IoT, machine learning, and artificial intelligence into the precision injection moulding process allows for real-time monitoring, predictive maintenance, and smarter production management. This evolution promises to increase efficiency and reduce downtime in manufacturing operations.
Choosing the Right Partner for Precision Injection Moulding
When selecting a precision injection moulding partner, consider the following criteria to ensure that you meet your business objectives:
- Experience: Choose a partner with a proven track record in precision injection moulding.
- Quality Assurance: Ensure that they follow stringent quality control processes to maintain product standards.
- Technology: Look for a manufacturer who utilizes the latest technologies and methods in their production processes.
- Customer Service: A responsive partner who prioritizes customer satisfaction can greatly enhance your project's success.
Conclusion
In summary, precision injection moulding is a game-changer in the world of metal fabrication. Its ability to produce high-quality, intricate parts quickly and cost-effectively makes it an essential technology for various industries. As the demand for precision and quality increases, the significance of this manufacturing process will only grow. Therefore, businesses looking to stay ahead must consider investing in precision injection moulding techniques to adapt to the evolving market demands.
For companies in the metal fabricators space, aligning with reputable partners like deepmould.net who specialize in precision injection moulding can lead to a profound transformation in production efficiency and product quality. Embracing this technology will ensure that your business stays competitive in an ever-evolving industry landscape.