CNC Lathe Parts Factories: The Backbone of Modern Manufacturing
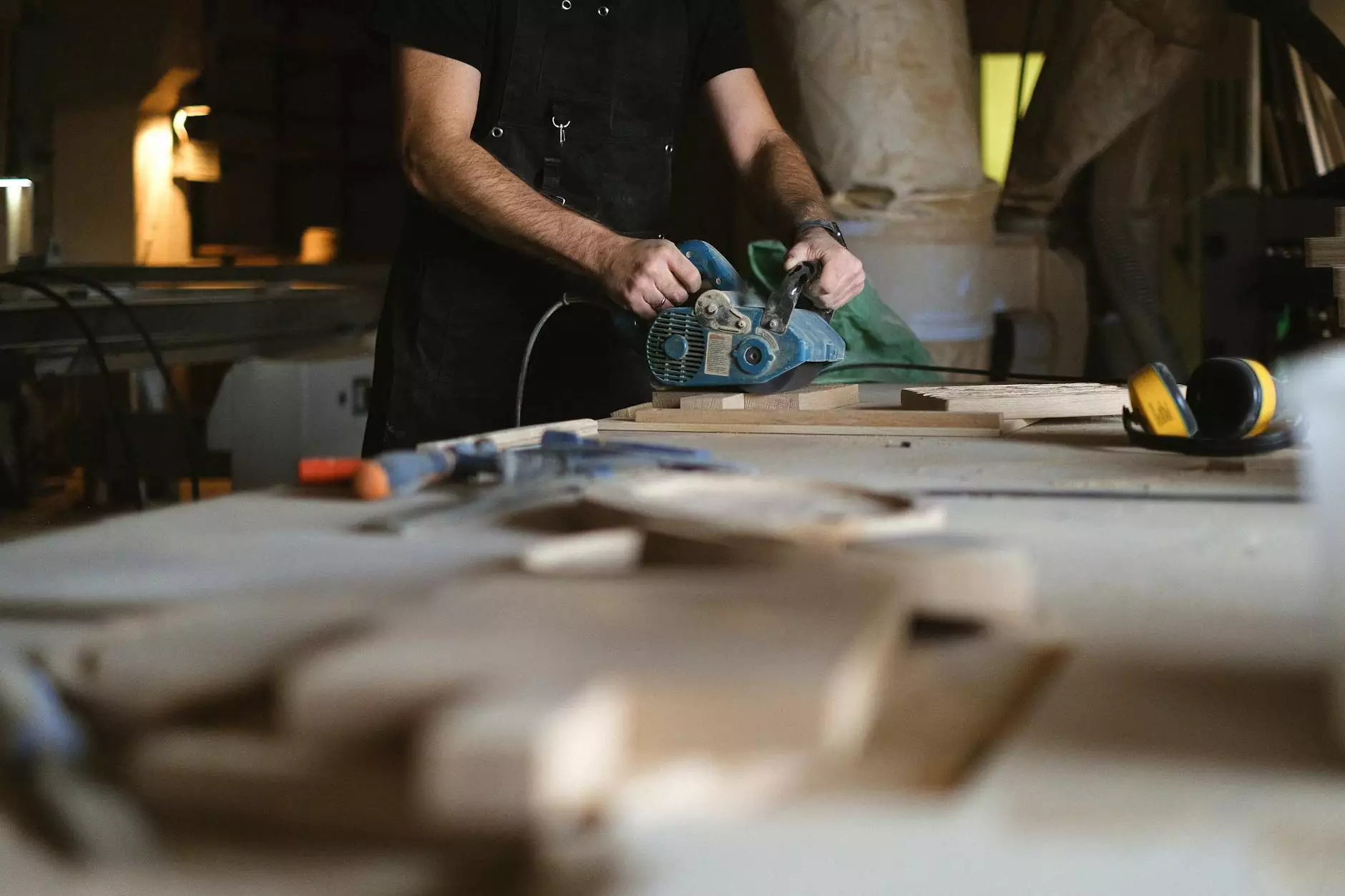
The CNC lathe parts factories play a crucial role in the manufacturing domain, serving as the backbone for various industries. Their importance cannot be overstated, as they offer precision-engineered components vital for numerous applications. In this article, we will delve into the intricacies of CNC machining, highlight the innovative practices employed by these factories, and explore how technological advancements are continuously shaping the future of manufacturing.
Understanding CNC Lathe Technology
CNC stands for Computer Numerical Control, a technology that revolutionizes the machining industry. Unlike traditional lathes, which require manual input for every operation, CNC lathes utilize computer programming to control their movements and functions. This advancement allows for increased accuracy and efficiency in producing complex parts.
The Role of CNC Lathes in Manufacturing
CNC lathes are primarily used to create cylindrical parts, including:
- Axles
- Spindles
- Bushings
- Housings
These components are essential in various industries such as automotive, aerospace, electronics, and medical devices. The precision of CNC machining ensures that each part fits perfectly into the larger assembly, significantly reducing the chances of errors and improving overall product quality.
Key Features of CNC Lathe Parts Factories
The success of a CNC lathe parts factory hinges on several critical features:
1. Advanced Machinery
Top-tier CNC factories invest in state-of-the-art machinery equipped with high-tech software. This not only enhances production efficiency but also elevates the quality of output. Machines that can perform multiple operations, such as turning and milling within the same setup, save time and minimize handling errors.
2. Skilled Workforce
A well-trained workforce is another asset of successful factories. Operators must understand both the mechanical aspects of lathes and the programming nuances of CNC technology. Continuous education and skill upgrades are crucial for keeping up with industry advancements.
3. Quality Control Processes
Quality assurance is paramount in CNC lathe parts production. Factories often implement rigorous quality control measures, such as:
- Regular inspections of machinery
- Use of precision gauges and measurement tools
- Performance audits of production processes
These protocols ensure that every piece produced meets or exceeds industry standards.
4. Automation and Robotics
The integration of automation and robotics in CNC lathe parts factories has transformed production capacities. Automated systems can handle repetitive tasks, allowing human workers to focus on complex decision-making processes. This balance enhances productivity while maintaining high-quality standards.
Innovations in CNC Lathe Parts Production
As technology continues to evolve, so do the techniques employed in CNC lathe manufacturing. Some notable innovations include:
1. Software Advancements
Modern CNC machines come equipped with sophisticated software that allows for higher-level programming and simulation capabilities. This enables engineers to visualize the entire production process before actual machining, thus identifying potential issues and optimizing performance.
2. 3D Printing Integration
3D printing technology is being increasingly integrated into CNC manufacturing processes. It allows for rapid prototyping of parts that can be manufactured later on CNC lathes. This not only accelerates product development but also reduces costs associated with traditional manufacturing.
3. Eco-Friendly Practices
Environmental sustainability is becoming a priority in manufacturing. Many CNC lathe parts factories are implementing eco-friendly practices such as:
- Recycling metal scraps
- Utilizing biodegradable lubricants
- Implementing energy-efficient machinery
These practices not only help in conservation but also enhance the factory’s reputation among consumers.
Navigating Challenges in CNC Manufacturing
Despite the many advantages of CNC machining, factories face several challenges:
1. Market Competition
The global market for CNC machining is highly competitive. Companies must continuously innovate and adopt the latest technologies to stay relevant. This necessitates significant investment in both machinery and workforce training.
2. Supply Chain Disruptions
Modern factories depend on a complex network of suppliers for raw materials. Disruptions, such as those seen during the global pandemic, can hinder production schedules and increase costs. Establishing reliable relationships with suppliers and diversifying sources are essential strategies for mitigating these risks.
3. Maintaining High Standards
Consistency in product quality is crucial. Any deviation from set standards can lead to costly recalls and damage to a company’s reputation. Therefore, investing in robust quality assurance systems is vital for maintaining credibility and maximizing customer satisfaction.
The Future of CNC Lathe Parts Factories
The future of CNC lathe parts factories is bright, with many trends pointing toward increased automation, improved precision, and sustainability. As industries continue to grow and diversify, the demand for high-quality machined parts will likely soar.
1. Increased Customization
With advancements in manufacturing technology, customization will become increasingly feasible. Customers will demand more bespoke solutions tailored to their unique requirements, promoting factories to adapt swiftly to these needs without sacrificing efficiency.
2. Smart Manufacturing
The concept of smart manufacturing, which integrates IoT and AI into production processes, is on the rise. This approach allows for real-time monitoring and predictive maintenance of machinery, optimizing production and reducing downtime.
3. Global Collaboration
As businesses look to expand their market reach, collaboration between CNC lathe parts factories across different regions will become commonplace. This collaboration can lead to shared best practices and new technological innovations, ultimately benefiting the global manufacturing landscape.
Conclusion
The importance of CNC lathe parts factories in today’s manufacturing ecosystem cannot be underestimated. They are the driving force behind precision engineering and innovation across various industries. By embracing advanced technologies, fostering a skilled workforce, and implementing sustainable practices, these factories will continue to thrive and shape the future of manufacturing.
For those looking to partner with a reliable CNC parts factory, consider Deepmould.net, a leader in the field of metal fabrication. Their commitment to quality, precision, and customer satisfaction makes them a top choice for CNC lathe parts manufacturing.