Transforming Innovation into Reality: The Role of a China Die Casting Mold Factory
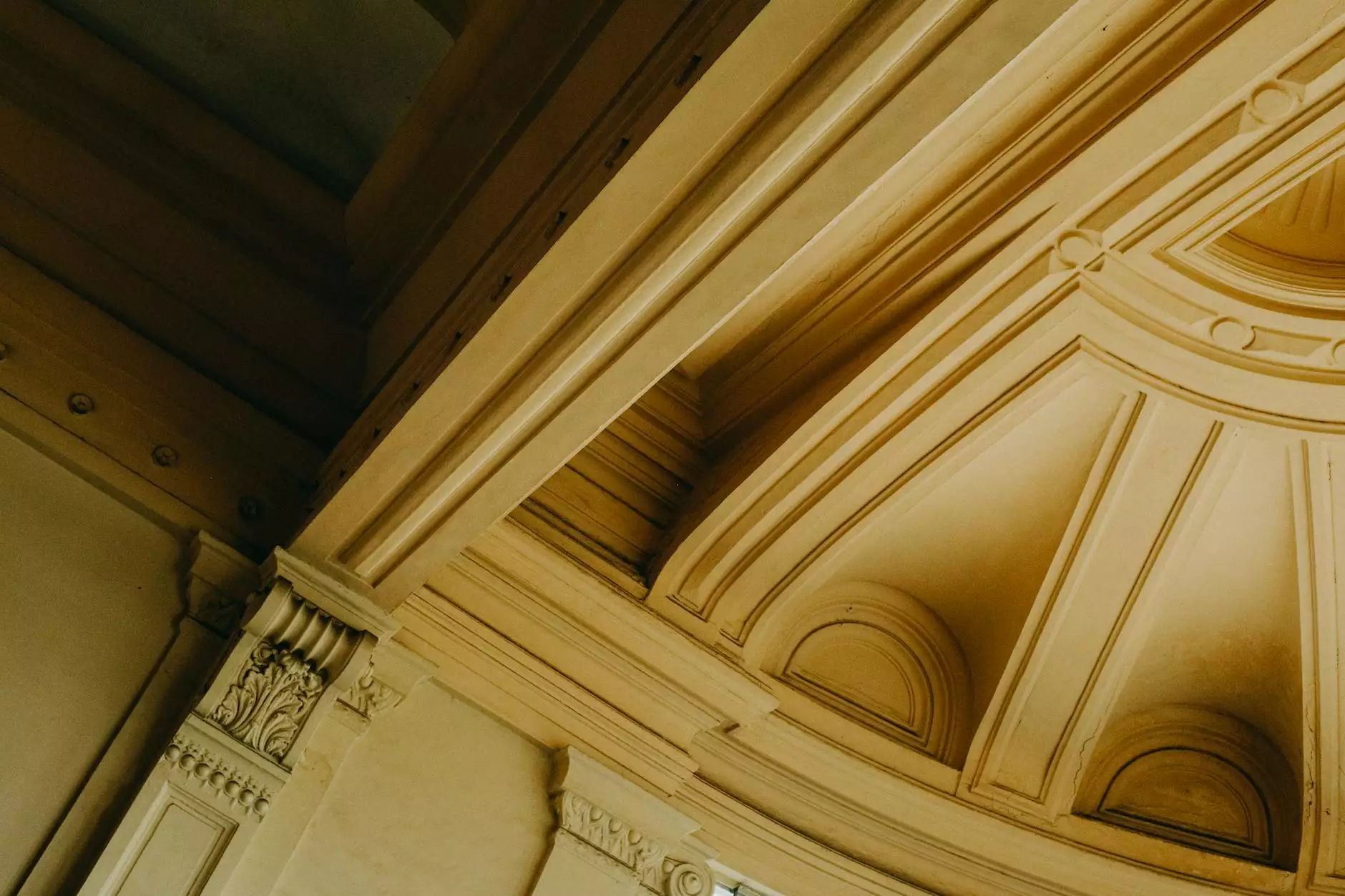
In the ever-evolving world of manufacturing, die casting stands out as a revolutionary process that allows for the creation of complex shapes with remarkable precision. A China die casting mold factory is at the forefront of this innovation, merging traditional manufacturing techniques with modern technology to produce high-quality metal components. This article delves into the intricate processes, advantages, and future trends of die casting, emphasizing the remarkable capabilities of a specialized die casting mold factory in China.
The Essence of Die Casting
Die casting is a metal-forming technique that involves forcing molten metal into a mold under high pressure. This method is especially favored for its ability to create detailed, intricate shapes that are consistent in size and finish. In a typical die casting process, the following steps are involved:
- Preparation of the Mold: The mold is crafted to exact specifications to ensure that the final product meets quality standards.
- Melting the Metal: The chosen metal, often aluminum or zinc, is melted to a specific temperature.
- Inserting and Pressurizing: The molten metal is injected into the mold under high pressure, allowing every detail of the mold to be filled.
- Cooling and Solidifying: The metal cools and solidifies quickly, leading to a strong and durable product.
- Mold Removal: Once cooled, the mold is opened, and the finished part is removed.
Key Benefits of Choosing a China Die Casting Mold Factory
Partnering with a China die casting mold factory provides numerous advantages that can enhance your manufacturing processes and product quality:
- Cost-Effectiveness: Manufacturing in China often yields significant cost savings due to lower labor and material costs.
- High-Quality Products: Advanced technologies and skilled labor contribute to producing highly precise and durable metal components.
- Rapid Turnaround Time: Efficient production methods allow for quicker delivery times, which is crucial in today's fast-paced market.
- Access to Advanced Technologies: Many Chinese factories are equipped with the latest die casting machines and technologies, ensuring that they meet international standards.
- Flexibility in Production: A well-established die casting factory can handle both large scale production runs and custom orders, meeting diverse client needs.
Innovations in Die Casting Technology
The die casting industry is continuously evolving, thanks to technological innovations that improve production efficiency and product quality. Here are some of the latest advancements you might expect from a top-tier China die casting mold factory:
1. Automated Processes and Robotics
Automation is reshaping the manufacturing landscape, and die casting is no exception. Factories are integrating robotics to:
- Enhance precision in the casting process.
- Reduce human error during handling and assembly.
- Increase overall production efficiency.
2. Improved Mold Design
With advancements in CAD (Computer-Aided Design) and simulation software, mold designs are more efficient than ever. This technology allows:
- For better cooling and heating distributions.
- Reductions in cycle times, thereby increasing productivity.
- Enhanced durability of the molds, leading to longer life spans.
3. Sustainable Practices
Today's manufacturers are more environmentally conscious. Leading die casting factories are implementing sustainable practices by:
- Recycling metallic scraps and using recycled materials.
- Exploring alternative energy sources for production.
- Implementing waste reduction strategies throughout the production process.
Industries Benefiting from Die Casting
Die casting is integral to numerous industries, providing solutions that are crucial for modern products. A China die casting mold factory services various sectors, including:
- Automotive Industry: Die casting produces components like engine blocks, transmission cases, and other critical car parts.
- Electronics: High-precision parts for electronic devices ensure reliability and performance.
- Aerospace: Lightweight yet strong components are vital for aircraft efficiency and safety.
- Home Appliances: From appliance casings to intricate inner components, die casting plays a significant role in production.
- Medical Equipment: Precision manufacturing is crucial for producing medical devices and surgical tools.
Challenges Faced by Die Casting Manufacturers
While the benefits are substantial, die casting manufacturers also face challenges that must be navigated for successful operations:
1. High Initial Costs
The upfront cost of creating molds can be significant, particularly for complex parts. However, this cost is often offset by the efficiency gained in mass production.
2. Design Limitations
Some design limitations exist. Factors like wall thickness and draft angles can impact the capabilities of the die. Collaborating with experienced designers can help mitigate these issues.
3. Environmental Regulations
Increasing scrutiny on environmental practices means die casting factories must adapt to comply with regulations, prompting a shift towards more sustainable manufacturing processes.
The Future of Die Casting Manufacturing
The future looks promising for die casting, especially within China die casting mold factories. With increasing demand for high-precision components and a market leaning towards sustainability, innovation will continue to drive this industry forward.
Trends to Watch In Die Casting
- Smart Manufacturing: The integration of IoT (Internet of Things) will enable smarter manufacturing processes with real-time monitoring and predictive maintenance.
- Expansion into New Materials: The exploration of new alloys and materials will enhance product performance and expand application ranges.
- Customization and On-Demand Production: As industries shift towards customization, die casting factories will increasingly focus on personalized production runs.
Conclusion: Choosing the Right Partner
In conclusion, selecting the right China die casting mold factory is critical for businesses looking to leverage the full potential of die casting technology. Factors such as quality, reliability, technological prowess, and customer service should all weigh heavily in your decision-making process. By partnering with a leading factory, you gain access to unparalleled manufacturing capabilities that can help propel your business to new heights.
At DeepMould.net, we pride ourselves on our commitment to excellence in metal fabrication. Our experience, technological advancements, and dedication to customer satisfaction ensure that we meet and exceed your die casting needs, providing solutions that empower your business. Connect with us today to discover how we can support your manufacturing endeavors with the precision and efficiency that define modern casting processes.